Detailed explanation of safety technology design for atmospheric pressure reactor
Category: Technical Documents
Date: 2024-05-14
Click: 422
Author: JZ
Collection:
Atmospheric pressure reactor is a common equipment in chemical production, mainly used for chemical reactions between liquid and solid, liquid and gas or liquid under atmospheric pressure conditions.Due to the potential involvement of hazardous substances such as high temperature, high pressure, flammability, explosiveness, and toxicity during its operation, ensuring the safe operation of the atmospheric pressure reactor is crucial. Jinzong Enterprise, with over 20 years of experience in the production, research and development of reaction vessels, will provide a detailed introduction to the safety technology design points of atmospheric pressure reaction vessels to ensure production safety and personnel health.
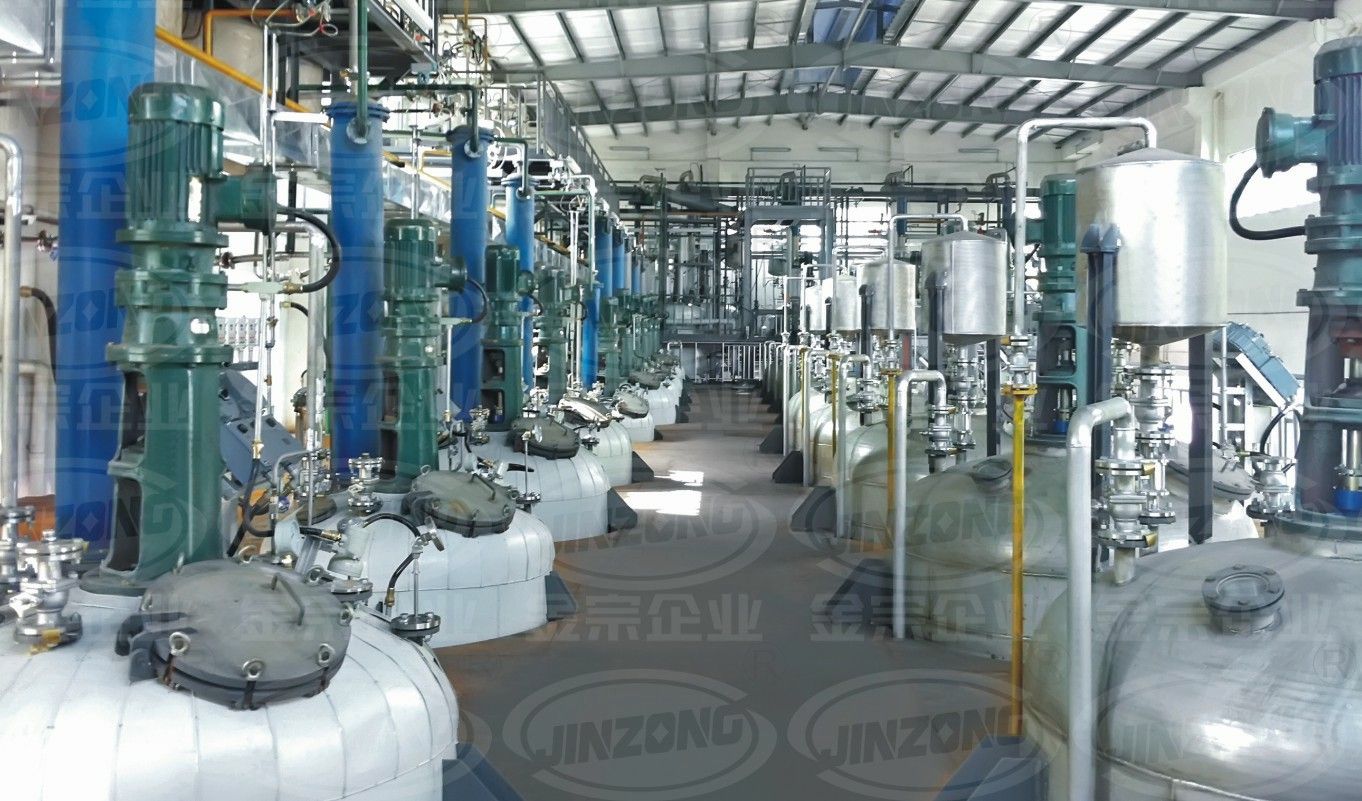
1. Material Selection and Strength Design
Material Selection: The material of the reaction vessel needs to be selected based on the characteristics of the reaction medium (such as corrosiveness, temperature, pressure), commonly including stainless steel, carbon steel, enamel, fiberglass, etc. For highly corrosive media, materials with strong corrosion resistance should be selected; In high-temperature environments, the thermal stability of the material needs to be considered.
Strength Calculation: Based on the working pressure, temperature, and internal and external loads borne by the reactor, accurate mechanical calculations are carried out to ensure that the shell has sufficient strength and stiffness to prevent rupture caused by overpressure or mechanical damage.
2. Temperature Control and Heating/Cooling System
Temperature Control: Accurate temperature control is the key to ensuring the smooth progress of the reaction. Atmospheric reactors are usually equipped with electric heating sleeves, steam heating, or external circulating heating/cooling systems, which are automatically adjusted through temperature controllers to prevent accidents caused by local overheating or excessive temperature differences.
3. Mixing System Design
The mixing system not only affects the reaction efficiency, but also an important part of safety design. Suitable agitator types (such as paddle, turbine, anchor, etc.) should be selected based on the properties of the reactants, and reliable sealing of the mixing shaft should be ensured to prevent material leakage. At the same time, set up overload protection devices to avoid equipment damage due to excessive mixing load.
4. Security Attachment Configuration
Pressure Release Device: Although the atmospheric reactor is designed for atmospheric operation, safety valves or rupture discs still need to be installed in case of abnormal pressure rise.
Emergency Shutdown System: Integrated with an emergency stop button in the control system, it can quickly cut off power and material supply in case of any abnormality.
Sight Glass and Lighting: Convenient for operators to observe the reaction inside the kettle and detect abnormalities in a timely manner.
Exhaust and Ventilation: Set up a good exhaust system to maintain air circulation in the workshop and reduce the accumulation of harmful gases.
5. Fire and Eexplosion Prevention Measures
Electrostatic Grounding: Ensure that the reactor and all metal components such as pipelines and valves are well grounded to prevent the accumulation of static electricity from causing sparks.
Explosion Proof Electrical Equipment:
Use electrical equipment that meets the explosion-proof level in explosive hazardous areas to reduce ignition sources.
Inert Gas Protection: For flammable reaction systems, inert gases such as nitrogen can be used to cover and reduce the risk of explosion.
6. Operating Procedures and Training
Develop detailed operating procedures, including equipment operation, maintenance, emergency response, etc., and provide regular training to operators to ensure they are familiar with equipment performance and safety operation knowledge.
In summary, the safety technology design of atmospheric pressure reactors is a comprehensive process that requires comprehensive consideration from multiple aspects such as equipment material selection, structural design, control system, and safety accessory configuration. At the same time, it is necessary to strengthen the safety awareness and skill training of operators in order to effectively prevent accidents and ensure production safety.