Category: Technical Documents
Date: 2024-04-24
Click: 505
Author: JZ
Collection:
一、Introduction
As an important chemical equipment,reactor is widely in Petroleum, Chemical, Pharmaceutical, Food and Other fields,it is used to realize the Mixing, Reaction, Evaporation, Crystallization and Other processes of materials.Among then,heating as a key link to control reaction temperature and promote the chemical reaction ,it mode and efficiency directly affect the overall performance and production efficiency of the reactor.With more than 20years of experience in reactor production,research and development design,Jinzong enterprise elaborate the common heating methods and working principles of the reactor for everyone,and carry out an in-depth analisis of their respective advantages and disadvantages,hoping to help you.
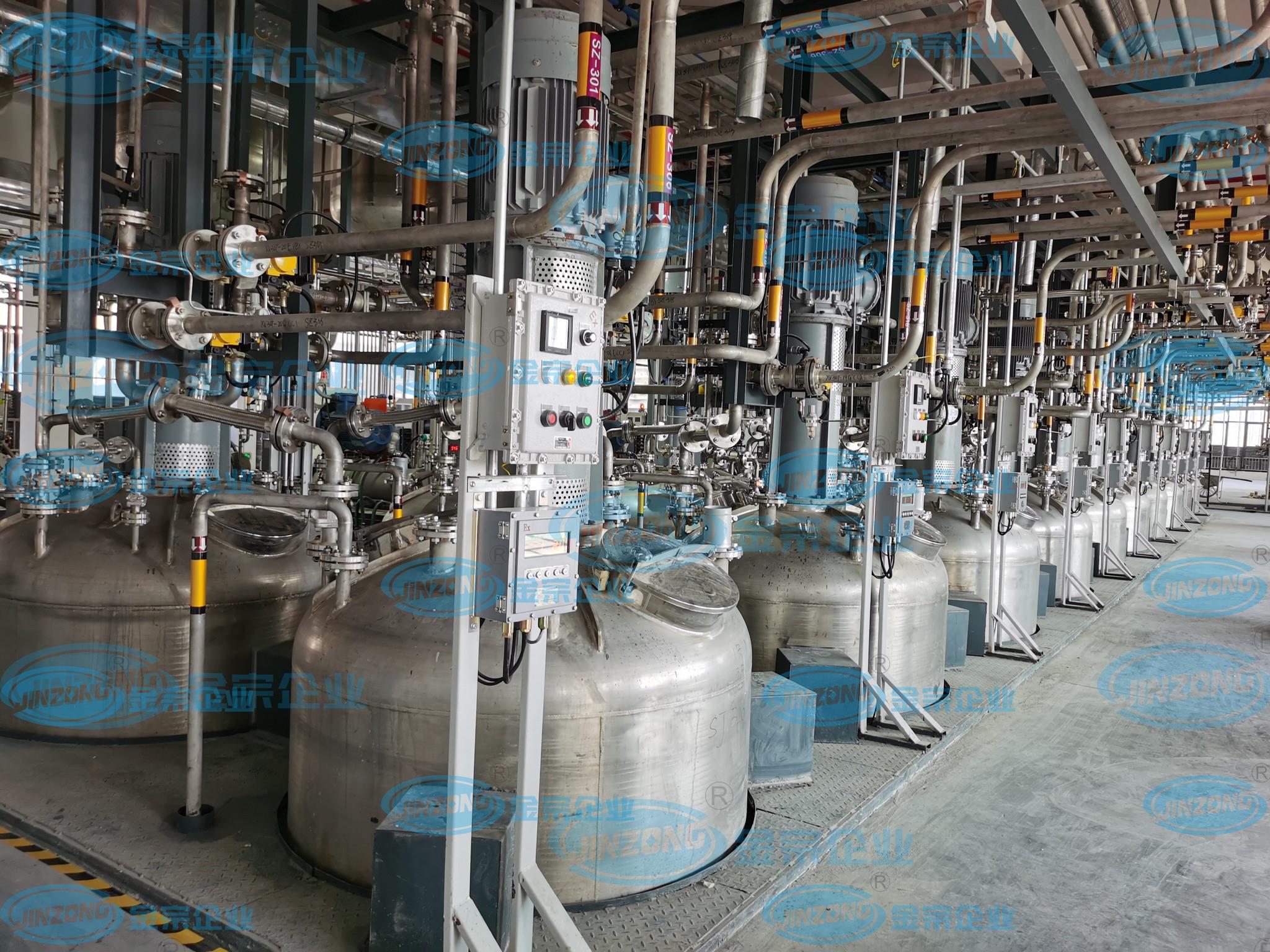
二、Heating Method of Reactor
Electrical Heating
Electric heating is by installing electric heating elements (such as Resistance Wires,Silicon Carbon Rods,PTC ceramics,etc.)inside or outside the reactor,using the current to generate heat through the resistance to heat the reactor body or transfer medium.According to the placement of the electric heating element,it can be divide into internal heat and external heat.
Principle:electric energy is converted into heat energy,and materials in the kettle are heated directly or indirectly.
Advantages:High thermal efficiency,fast heating speed,precise temperature control,no pollution,easy to achieve automatic control.
Disadvantages:Large power consumption,for large capacity or high temperature reaction may cause power supply pressure;Electric heating elements are susceptible to corrosion and need regular inspection and maintenance;Explosion-proof design should be considered for materials with explosion risk.
Steam Heating
Steam heating is the use of steam as heat sources,which enters the jacket or coil of reactor kettle through steam pipeline and carries on heat exchange with the materials in the reactor to achieve heating purpose.
Principle: The steam condenses and releases heat in the jacket or coil,and the heat is transferred to the material in the kettle through the wall.
Advantages:Stable heat source ,relatively low cost, siutable for large-scale continuous production;Steam has a certain self-purification ability,less corrosion of equipment.
Disadvantages: Need to be equipped with steam boiler or steam pipe network,equipment inestment and operating costs are high;the heating rate is relatively slow,and the temperature control is not as accurate as electric heating;there are steam leakage and condensate discharge problems.
Oil bath heating
Oil bath heating is to send the heated heat conduction oil into the jacket or coil of the reactor through the circulating pump, and heat is heated through the heat exchange between the hot oil and the materials in the reactor.
Principle: The electric heater heats the thermal oil to the set temperature, and the hot oil circulates in the jacket or coil to transfer the heat to the material in the kettle.
Advantages: stable temperature control, good safety performance, especially suitable for high temperature reaction; High thermal efficiency, small heat loss; No steam leakage problem.
Disadvantages: The initial heating speed is slow, and it takes some time to preheat; Heat transfer oil system is complex, equipment investment is large; Heat conduction oil is easy to age and needs to be replaced regularly.
Far infrared heating
Far infrared heating is the use of far infrared radiation elements generated by far infrared radiation, directly through the reactor wall to heat the material.
Principle: After the far-infrared radiation element is energized, a large number of far infrared rays are generated, and the far infrared rays are absorbed by the material and converted into heat energy to achieve heating.
Advantages: uniform heating, high thermal efficiency, significant energy saving effect; No contact heating, little impact on material properties, no pollution.
Disadvantages: The equipment cost is high, and the infrared absorption performance of the material has certain requirements; For large capacity reactors, radiation heating may be uneven.
三、Conclusions
The heating selection of reactor should concider the reaction conditions(such as temperature ,pressure,material properties etc,.production scale,energy supply,economy and other factors.Electric heating is suitable for small,precise temperature control and high environmental protection requirements.Steam heating and oil bath heating are suitable for large-scale,continuous production and high-temperature reaction occasions;Far infrared heating is suitable for special applications that require high heating uniformity and material purity.Reasonable selection and use of heating methods can not only effectively improve the reaction efficiency, but also ensure the safety and stability of the production process, reduce energy consumption, and meet the development trend of green chemical industry. If you want to know more about the reactor, please contact JinZong for detailed communication or field visit.