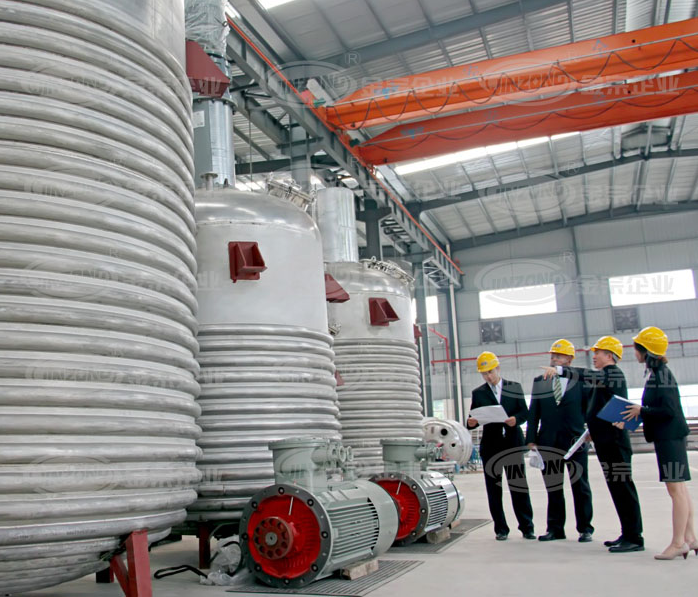
Magnetic reaction kettle is a typical innovation in the application of magnetic drive devices in reaction equipment. It fundamentally solves the problem of shaft seal leakage that was previously insurmountable by packing seals and mechanical seals. This device has no leakage or pollution, and is currently the most ideal device for chemical reactions under high temperature and high pressure in China, especially for chemical reactions in flammable, explosive, and toxic media, demonstrating its superiority. While using it, we cannot ignore the safety issues it brings. Next,Jinzong Enterprise will introduce you to the relevant knowledge of safe use of magnetic reaction kettels.
1、 Precautions before use
Sealing Performance
Magnetic reaction kettle belongs to precision equipment, which adopts a conical contact sealing form through sealing rings, and achieves the purpose of sealing by tightening the main bolts to press them against each other. Therefore, special care must be taken for the sealing cone surface to avoid damage caused by various collisions. When installing the cover, first place the reactor body and then carefully place the cover in a fixed position on the body. When tightening the main bolts, they must be tightened diagonally and symmetrically in multiple steps, with even force. The cover is not allowed to tilt to one side to achieve good sealing effect, and the specified tightening torque should not be exceeded to prevent the sealing surface from being squeezed or accelerated wear. All threaded connectors need to be coated with oil or oil mixed with graphite during assembly. If the sealing surface is damaged, it needs to be reprocessed and repaired to restore good sealing performance.
Sealing Operation
The inlet and exhaust valves are sealed with needle valves. When closed, simply gently rotate the valve needle to press the sealing surface tightly to achieve good sealing. Excessive force is prohibited to avoid damaging the sealing surface.
Heating and Pressurization Test
Before using the magnetic reaction kettle, a heating and pressure sealing test should be conducted. The test medium can be air or nitrogen, but it is best to use inert gas. The use of oxygen or other flammable and explosive gases is strictly prohibited. Heating and pressure boosting must be carried out slowly. The heating rate shall not exceed 80 degrees per hour. During pressure testing, connect the inlet valve of the magnetic reaction kettle to the compressor (or high-pressure pump) using a connecting pipe. The pressure increase must be carried out in stages, with a spacing of 20% of the working pressure. Each level should be stopped for 5 minutes, and when the test pressure is raised, it should be stopped for 30 minutes to check the sealing condition. The test pressure is 100%-105% of the working pressure. If a leak is found, the pressure should be reduced first, and then the nuts and joints should be tightened appropriately. It is strictly prohibited to tighten the nuts and joints under high pressure.
Cooling Process
During the reaction process, rapid cooling and rapid heating are prohibited to prevent excessive temperature stress from causing cracks in the reactor body. After the reaction is completed, cooling and cooling should be carried out first. Water cooling (exothermic reaction) or air cooling can be used, and then high-pressure gas in the kettle can be released to reduce the pressure to atmospheric pressure. Then, the bolts should be symmetrically and evenly loosened and removed. During the opening process, special attention should be paid to protecting the sealing surface, and the kettle cover should be lifted evenly to avoid damage caused by collision between the sealing ring of the kettle cover and the kettle body.
Subsequent Processing
After each operation, the residue on the kettle body and lid should be removed. All sealing surfaces on the magnetic reaction kettle should be cleaned regularly and kept dry. It is not allowed to clean with hard objects or soft objects with rough surfaces.
2、 Safe Usage Regulations
Preparation Before Use
Before feeding, the reaction kettle should be checked for contamination. The inner walls, stirring, cooling coils, temperature probe sleeves, and joint surfaces of the magnetic reaction kettle should be cleaned with ethanol, and then rinsed with distilled water. After rinsing, cotton or silk cloth dipped in ethanol should be wiped clean to prevent cross contamination of materials. Before use, it is necessary to check whether all valves are unobstructed, especially the pressure gauge and explosion-proof membrane pipe openings. For the intake duct, special attention should also be paid to whether there is any blockage. If there is material contamination or blockage, the duct and intake branch should be removed from the kettle cover, cleaned, and then installed.
Sealing Inspection
After cleaning is completed and the kettle body is dry, a sealing inspection should be conducted first. Place the kettle body into the heating furnace, align the protruding part with the groove, and gently rotate the kettle body. After stabilizing, slowly and steadily close the kettle body and kettle cover. Special attention should be paid to protecting the sealing surface to avoid damage caused by collision between the kettle cover and the sealing ring of the kettle body. After covering, check whether the upper and lower interfaces of the reaction kettle are aligned. Gently rotate the kettle cover to confirm that it is flat and the sealing ring is in good contact. After adding a gasket, start screwing in.
Precautions For Screw Installation
When installing screws, be sure to seat them in the correct position. Tighten them by hand first, and then use a torque wrench to symmetrically place them in a cross shape to avoid uneven force distribution. Do not twist the screws into place at once. Tighten the diagonal screws multiple times and gradually apply force to tighten symmetrically.
Air Tightness Inspection
When checking the airtightness, it is necessary to first check whether each valve (solid feeding port, kettle cover exhaust valve, intake valve, etc.) is tightened (just hold on, do not use too much force). After adjusting the mixing switch and speed control heating switch of the controller to zero, turn on the power supply and display switch of the control box.
Pressure Testing Operation
一、Connecting Nitrogen Gas
Connect the nitrogen cylinder to the inlet of the magnetic reaction kettle through a conduit and tighten the relevant screws. Open the main valve and partial pressure valve of the nitrogen cylinder, first adjust the pressure of the partial pressure valve to the required pressure for the experiment, then open the inlet valve of the reactor to slowly charge the gas into the reactor. When the pressure value displayed on the reactor is the same as the set pressure on the nitrogen cylinder and no longer changes, sequentially close the inlet valve of the reactor and the outlet valve of the nitrogen cylinder, record the pressure value displayed on the reactor, and observe whether there is any change in pressure after half an hour.
二、Check For Air Leakage Points
If a significant downward trend is observed in pressure, the leak point should be checked. Use soapy water to identify potential leaks in the magnetic reaction kettle. The key inspection area is the interface between the magnetic reaction kettle cover and the inlet pipe, outlet pipe, and pressure gauge; The needle valve interface at the inlet and outlet, the sealing ring between the kettle body and kettle cover, and the thermometer probe socket. If air leakage is found, the pressure should be released first, and the corresponding leakage point should be tightened before pressurizing and testing for leakage. After checking for no leakage issues, release the pressure and clean the soap water with deionized water.
三、Turn Off Nitrogen Gas
Ensure that the pressure inside the kettle is completely released, close the main valve and pressure divider valve of the nitrogen steel cylinder, and release the residual pressure in the pipeline. Use a torque wrench to loosen the main nut in a symmetrical cross shape, slowly and steadily separating the kettle body from the kettle cover. Special attention should be paid to protecting the sealing surface to avoid damage caused by collision between the kettle cover and the sealing ring of the kettle body.
Feeding Operation
After the pressure test is completed, the feeding operation can be carried out. Add reaction materials and solvents to a clean and dry magnetic reaction kettle, and seal the kettle body and lid according to the above operation.
Inspection Work
Check if all valves (solid feeding port, kettle cover exhaust valve, intake valve, etc.) are tightened (just hold on, do not apply too much force), adjust the mixing switch and speed control heating switch of the controller to zero, ensure that the thermocouple has been inserted into the kettle cover and can display temperature changes normally, and then turn on the power supply and display switch of the control box. After turning on the cooling water connected to the mixing shaft, turn on the mixing switch and control the mixing speed through the speed controller to start mixing.
Adjusting Nitrogen Gas
Connect the nitrogen cylinder to the inlet of the magnetic reaction kettle through a conduit and tighten the relevant screws. Open the main valve and pressure divider valve of the nitrogen cylinder, first adjust the pressure of the pressure divider valve to about 1MPa, then open the inlet valve of the reaction vessel to slowly charge the gas into the reaction vessel. When the pressure value displayed on the reaction vessel is the same as the set pressure on the nitrogen cylinder and no longer changes, close the inlet valve of the reaction vessel. After stirring for about 3-5 minutes, open the exhaust valve to vent. After the vent is complete, close the exhaust valve. Repeat the inflation and deflation process 3-5 times to ensure there is no residual pressure in the kettle, then close the exhaust valve.
Introducing Hydrogen Gas
1、Pipeline Connection
Close the main valve and partial pressure valve of the nitrogen cylinder, and empty the residual pressure in the pipeline. Disconnect the connection between the magnetic reactor and the nitrogen cylinder, connect the magnetic reactor and the hydrogen cylinder through the pipeline, and tighten the relevant screws.
2、Hydrogen Pressure Regulation
Open the main valve and pressure divider valve of the hydrogen cylinder, first adjust the pressure of the pressure divider valve to about 0.5-1MPa, then open the inlet valve of the reactor to slowly charge the gas into the reactor. When the pressure value displayed on the reactor is the same as the set pressure on the hydrogen cylinder and no longer changes, close the inlet valve of the reactor. Connect the exhaust valve outlet to the outside through a pipeline, stir for about 3-5 minutes, then open the exhaust valve to vent. After venting, close the exhaust valve. After repeated inflation and deflation for 3-5 times, adjust the hydrogen cylinder pressure divider valve, adjust the pressure to the pressure required for reaction, and then slowly charge the gas into the reactor until the pressure indicated by the pressure gauge is consistent with the pressure required for the experiment. Close the inlet valve, the hydrogen cylinder main valve and the pressure divider valve.
3、Pre Heating Inspection
Check again with soapy water whether the air inlet and exhaust valve are leaking, and ensure that there is no hydrogen leakage before turning on the heating switch of the controller. Adjust the set reaction temperature step by step to prevent excessive heating temperature, and adjust the voltage to a reasonable range to ensure that the heating speed does not exceed 80oC/h. Run the heating program and start the reaction.
4、Parameter Change Control
After the reaction begins, close attention should be paid to the changes in various parameters (pressure, temperature, speed) in the reaction, especially the changes in pressure. Once abnormalities are found, the heating switch should be immediately turned off and department leaders should be reported. If the temperature is too high, cooling water can be connected to the cooling coil for cooling treatment; If the pressure is too high, it can be cooled down or vented through the exhaust valve. When venting hydrogen, it must be discharged outdoors through pipelines!
Sampling Control During Reaction
During the reaction process, if sampling is required, the material can be discharged through the inlet for analysis, but it must be ensured that the reaction system is homogeneous and there will be no solid precipitation. If heterogeneous catalysts such as palladium carbon or Raney nickel are used in the reaction, the stirring should be stopped before sampling and allowed to stand for about 10 minutes before sampling. If multiple sampling and analysis are required, the first part released from the pipeline is the residue in the pipeline, which cannot reflect the actual reaction situation in the reactor. About 20 milliliters should be released first before sampling and analysis.
Post Reaction Operation
After the reaction is complete, turn off the heating, set the temperature to room temperature, naturally cool down or cool down by passing cooling water through the cooling coil. When cooling to below 40oC, open the exhaust valve of the reaction kettle, slowly release the pressure completely, and use a torque wrench to loosen the main nut in a symmetrical cross shape. Slowly and steadily separate the kettle body from the kettle cover, paying special attention to protecting the sealing surface to avoid damage caused by collision between the kettle cover and the sealing ring of the kettle body.
Cleaning Of Reaction Kettle
Take out the kettle body, pour out the materials, and wash all the materials inside the kettle with solvent. Then, wash the kettle body, kettle cover, and sampling pipeline in sequence with ethanol and water, and wipe the sealing cone surface clean with a soft cloth or paper. Cleaning should be carried out immediately after discharge to avoid difficulties caused by solvent evaporation. After cleaning, place the kettle body and lid in a ventilated area to dry.
3、 Other Precautions
1. It is necessary to strictly follow the regulations when operating the reaction kettle, and it is not allowed to operate alone. During the experiment, two or more people are required.
During the pressure vessel operation, turn on the ventilation fan to ensure good ventilation.
When there is pressure inside the reactor, it is strictly prohibited to twist the nut or strike the magnetic reaction reactor.
4. At the connection between the front and back nuts (intake pipe, exhaust pipe, and branch pipe connecting the pressure gauge to the kettle cover), only the nuts should be turned and the two sealing surfaces should not rotate relative to each other.
5. Observe the reading on the pressure gauge at all times during operation, and it is strictly prohibited to use the kettle in case of overheating and overpressure.
If there is any air leakage during the experiment, immediately stop heating and the experiment. It is strictly prohibited to twist the nut at high temperatures.
7. Don't leave during the experiment.
8. The reaction kettle is not resistant to strong acids, and strong acids such as hydrochloric acid, sulfuric acid, and nitric acid are prohibited in the reaction solution.
9. Prior to use, the consent of the person in charge must be obtained. Anyone using the kettle must first carefully read the instructions.